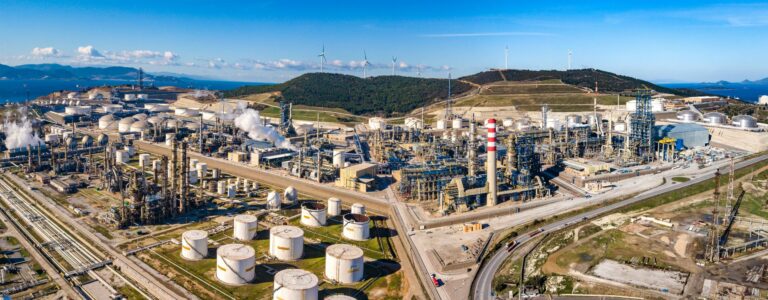
Oil&Gas
BAPCO Modernization Program
The Bapco Modernization Programme (BMP) is on track to become one of Bahrain’s most significant projects to date.
Located on Bahrain’s Eastern coast, the project aims to expand the capacity of the existing Sitra oil refinery from 267,000 to 360,000 barrels per day (BPD). Additionally, it seeks to enhance energy efficiency, maximize the utilization of heavy crude oil components, diversify product offerings, and ensure compliance with environmental standards.